About Us
ABOUT US
THE HISTORY OF SATAVA ART GLASS
The art glass that Richard creates is based in nature themes and motifs. When first starting out in the late seventies he mostly worked in the art nouveau technique, like many, because that was the accepted art glass style at that time. Just a few years later his work took off into a different direction, incorporating more of his own style, creating new looks in pictorial nature scenes with designs like the Harvest Moons, Mt. Shasta, floral lines, as well as, a series depicting images of Native American drawings. All these designs have evolved throughout the eighties and nineties, and continue to be created with new colors, shapes and inspiration.
During most of the 1990s he started to focus more attention on ocean life and nautical themes, creating the Moon Jellyfish and Nautilus series. Stemming from a visit to the Monterey Bay Aquarium, which enabled him to view jellyfish in an exceptional setting, much like viewing art at a gallery, he knew then that he needed to capture the nature of the jellyfish in glass. After spending three years experimenting with various formulas to achieve the translucent colors needed to make the jellyfish, finally by 1995 the series was ready for display. The Moon Jellyfish fast became one of his most successful creations and since that time has been displayed and sold all over the country by various galleries and aquariums.
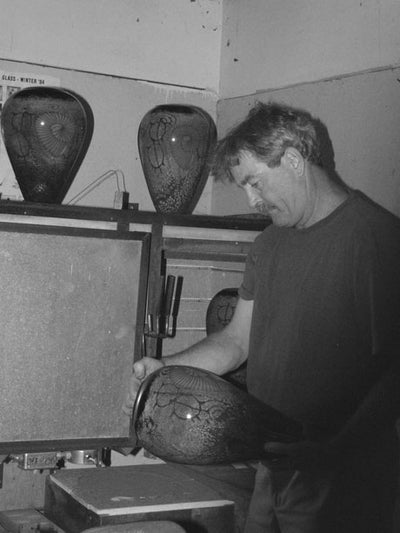
OUR PROCESS
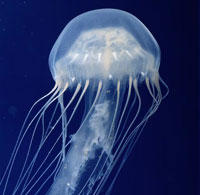
STEP ONE - INSPIRATION
Once Rick has an inspiration, like seeing the jellyfish at the Monterey Bay Aquarium or the bamboo that is just outside the studio, he does light sketches, thinking about the colors or the techniques necessary to make the idea work in glass. After many prototypes he continues to build on the concept until the design best encapsulates his original inspiration. Once this is achieved the process for everyday production of the work begins.
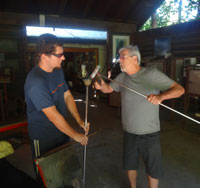
STEP TWO - PRODUCTION
The process can vary depending on each design. When making a jellyfish sculpture, we start with a gather of clear glass on a blowpipe. Then colored glass is gathered and trailed over the clear to form the tentacles, followed by rolling and picking up colored frit glass for the underskirt of the dome. Lastly the dome color is dropped on top, then continuously shaped and formed, adding clear layers, and reheating the glass until it is done.
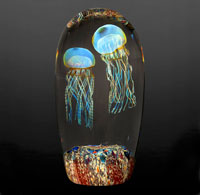
STEP THREE - FINISHING
At this point it is removed from the pipe and put in an annealing oven that will slowly cool it down over 24 hours. After the annealing process the piece is ground, polished, signed and numbered, then it is logged into ledger books that we keep permanently. At this point it is brought over to our shipping area where it is examined for quality, thoroughly cleaned and boxed with registration card, then shipped out to destinations all over the world.
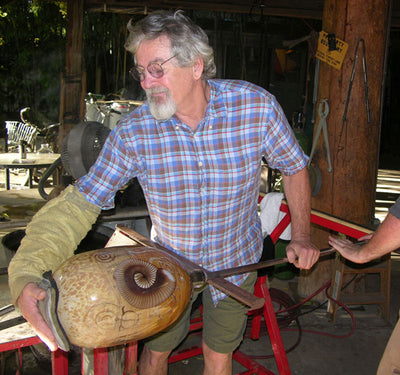
MEET THE TEAM
OWNER AND CREATOR, RICK SATAVA
Richard Satava was introduced to glassblowing in 1969 while at Oceana High School in Pacifica, California. He subsequently studied art and glassblowing at the College of San Mateo and California State University, Chico. As important as the skills that he learned while taking courses was the experience he received at California State University, Chico by being a technician for their glass shop. In 1977 he established his own Northern California glass studio called Satava Art Glass.
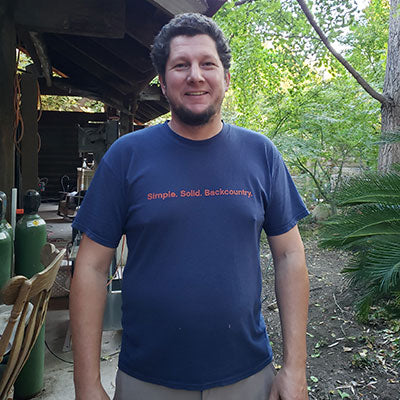
Production Manager
Mark Del Fava
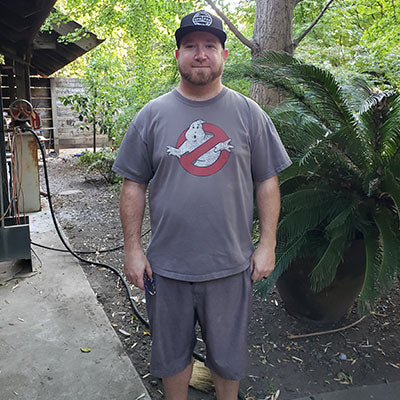
ASSISTANT PRODUCTION MANAGER
Wyatt Campbell
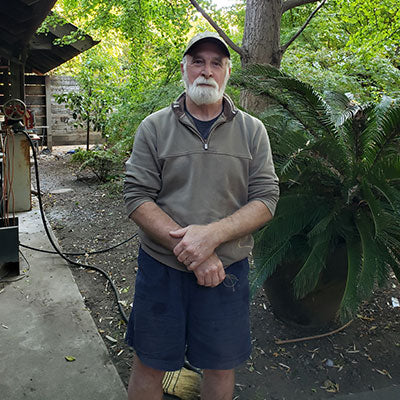
Cold Work Manager
Jim Radey
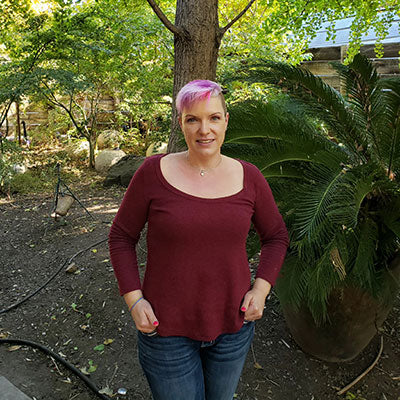